Boost wear resistance
Do you work with mining, slurry handling or other applications in which wear resistance is critical? How much will a shutdown due to a faulty tool, crusher, pump or another component cost you? Now imagine doubling or tripling the lifetime of critical components exposed to abrasive or erosive media – without having to resort to cemented carbides or facing the limitations of tungsten carbide overlays. The HIP process allows you to combine different material properties for cost-effective impact.
The perfect combination
For example, you might use a tough base metal and then combine it with a hard, wear-resistant surface. The good thing about HIP, is that regardless of the types of powder grades used, the PM process allows for excellent bonding to the substrate. The process lets you clad virtually any component with a highly wear-resistant material, at unlimited thickness, in any position, and with excellent bond strength. HIP can also be used to diffusion bond cemented carbides to steel with a bond strength more than four times as good as induction brazing. MTC offers a number of well-known, wear-resistant materials as well as proprietary powder alloys that are specifically aimed at very high wear-resistance.
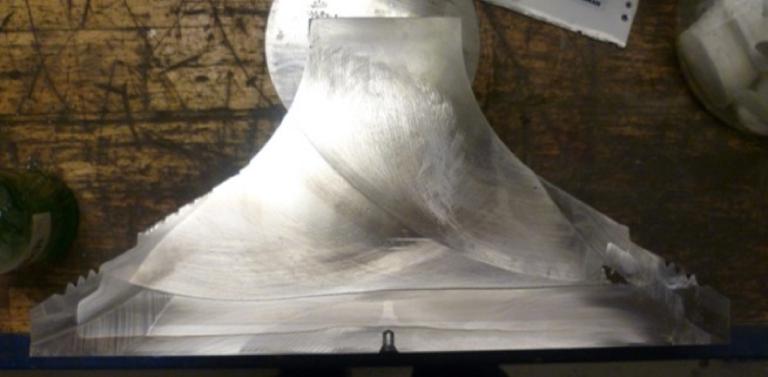
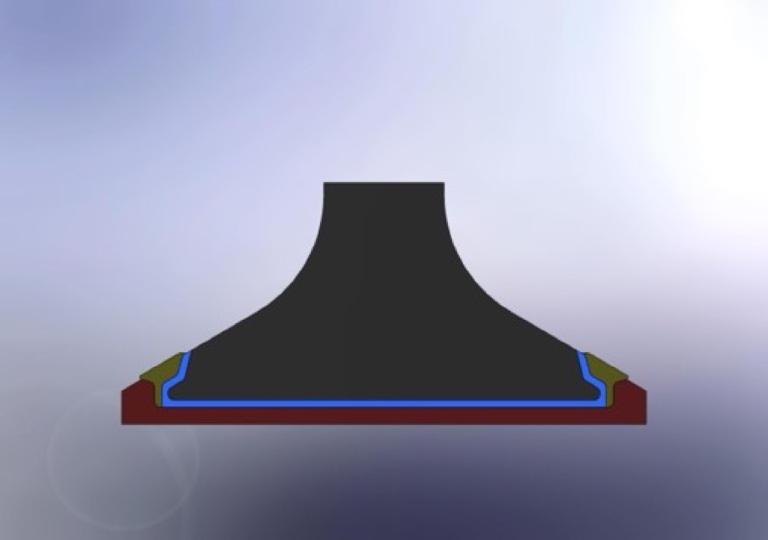
Crusher teeth
Mechanical components like crusher teeth and hammer heads in crusher plants are areas where HIP-based components are improving wear resistance every day – leading to added safety and reduced risk of unscheduled maintenance.
Tool steels
Tool steels are another area where HIP processing can enable thick, homogeneous, crack-free formations, coatings or multi-compounds on the hard facing to reduce wear. It can also be manufactured as monolithic pieces for the manufacturing of tools. One of the biggest threats to highly stressed tool steels is the presence of non-metallic inclusions and coarse carbides – a risk that is vastly reduced by the use of HIP due to its dense, homogenous material with minimal inclusion content and very small carbides.